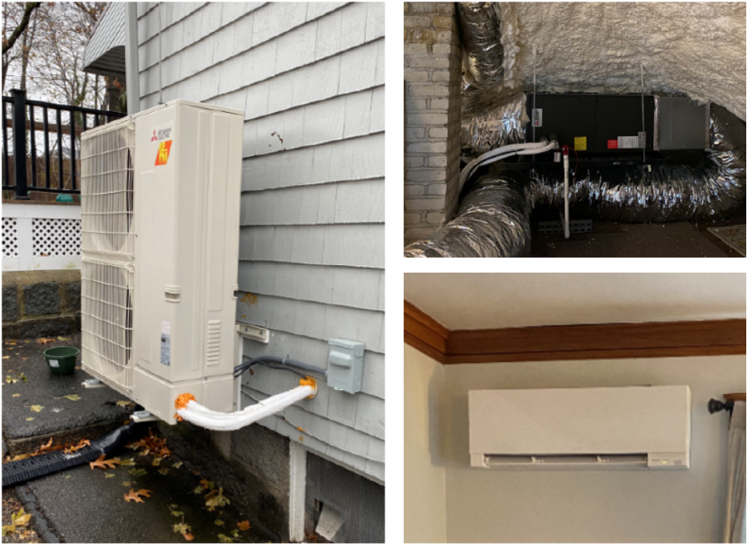
MassCEC is still accepting new applications for our whole-home air-source heat pump pilot through December 18, 2020. Projects will have an additional six months (retrofits) to one year (new construction) to install the heat pump. If you are thinking about a whole-home air-source heat pump system and you have any question please reach out to me.
The pilot launched in May 2019, and so far we have awarded a total of $266,250 to 84 projects out of an available budget of $500,000. Of those 84 projects, 53 are existing building retrofits, 7 are gut rehab projects, and 24 are new construction. See our previous monthly blog updates for more information about the pilot.
For the September pilot update, I’d like to share some updated data on project costs, as well as a case study.
Whole-Home Heat Pumps Costs
I discussed project costs in the January blog update when we had 31 approved projects. Now that we have a few more projects (currently 84 approved projects), I want to come back to this crucial topic. While 84 projects is still a very small sample size, I want to share some of the trends that we’ve been seeing. We are seeing higher costs in this pilot than I expected. In the table below, you can see that our average project cost is over $6,600 per ton of heat pump capacity at 5°F. In MassCEC’s previous air-source heat pump rebate program that was open to supplemental heating projects, the average cost per ton of capacity (at 5°F) was $3,900 for projects submitted in 2018 and 2019. I suspect that the major driver of the pilot’s higher costs is that whole-home heat pump systems require more expensive configurations that supplemental systems to distribute heat to the full home: either more smaller ductless heads or ductwork, both of which are expensive. Our previous rebate program was almost entirely ductless projects, very few of which were whole-home systems. Additionally, for whole-home systems, customers or installers may be likely to select more expensive features like floor mounted indoor units or wall-mounted thermostats. Designing a whole-home system versus a supplemental heat pump requires more upfront work from an installer, which adds to the cost. I am hopeful that this cost premium will shrink as installers become more accustomed to designing whole home heat pump configurations.
Project Type |
Number of Projects in MassCEC Pilot |
Average Conditioned Square Footage of Home |
Average Heat Load (BTU/SF) |
Average Cost per Ton of Heat Pump Capacity |
Average Project Cost
|
Median Project Cost |
---|---|---|---|---|---|---|
Existing Building |
53 |
1590 |
23 |
$6,723 |
$21,479
|
$18,998 |
Gut Rehab |
7 |
1204 |
21 |
$4,953 |
$12,315
|
$12,414 |
New Construction |
24 |
1694 |
13 |
$6,951 |
$14,349
|
$15,900 |
Total |
84 |
1588 |
20 |
$6,640 |
$18,678
|
$16,316 |
High upfront costs can be a barrier to homeowners retrofitting their home with heat pumps, although for homeowners looking to add cooling heat pumps may be the most affordable package. A 2018 study conducted by Navigant for Mass Save estimated that new natural gas furnaces cost around $4,000 to $6,400 installed while new natural gas boilers cost around $6,000 to $9,500 installed. These costs assume that a home already has ductwork or baseboards/radiators and the new fossil fuel equipment can be a drop-in solution. Once you consider the cooling benefit of heat pumps, the cost of a whole-home heat pump becomes more comparable to the alternatives. A 2018 memo from Navigant for Mass Save estimated that the average cost of an air-conditioner was around $4,100 per ton. The average heat pump capacity in the whole-home pilot is just under three tons, which would translate to around $12,000 for adding air conditioning to these homes, which places the cost of whole-home heat pump systems more on par with traditional heating and cooling options. That sounds like a high price for a replacement air conditioner to me, but a very low price for a home that needs entirely new duct work built.
Looking at these cost comparisons reinforces my belief that a whole-home heat pump system will be the right solution for some customers versus maintaining the home’s existing fossil fuel equipment. It could definitely be a cheaper option to just get a supplemental heat pump that serves the main space or several key spaces in a home, but for homeowner that are looking to put heat pump distribution throughout their home, it may make economic sense to design a whole-home system, so that the homeowner does not have to pay for a new fossil fuel furnace or boiler.
However, one factor currently working against heat pumps is the current low price of natural gas, which means that even if a whole-home heat pump system costs the same to install as a natural gas heating system plus air conditioning, it will cost more to operate at current gas and electric prices. Operating costs of heat pumps look better against oil, propane, and electric resistance, which is one reason Mass Save offers generous incentives for switching from these fuels to heat pumps.
For a final thought, I’ll highlight that the economics of whole-home heat pumps make the most sense on the new construction side, where the home can be designed for heat pumps from the start. With stricter building codes and better insulated new homes, builders can install a smaller heat pump system to meet the needs of the home, and the heating costs for any fuel will be minimized which reduces the operating cost benefit of today’s cheap natural gas. All in all for new construction, heat pumps can be the cheapest way to provide heating and cooling equipment for a home, especially when you factor in the savings from not running a natural gas line to the home or development.
For next month’s blog, I’ll do a deeper dive into the prices we’ve been seeing for retrofit projects with ducted versus ductless indoor distribution.
Project of the Month: Boston Home with Mixed Ducted & Ductless Multi-head
Starting with last month’s blog, I’m profiling one pilot project every month to share personal stories of what it’s been like for customers to live with whole-home heat pump systems. This month, I want to feature a 1300 square foot home located in the Dorchester neighborhood of Boston. The home was built in the 1930s, and has been upgraded to have double pane windows, wall insulation, and a spray-foamed attic. The home previously had a natural gas steam boiler and used window units for air-conditioning. Through the pilot, the homeowner installed a Mitsubishi MXZ-4C36NAHZ, which is a multi-head heat pump that can have up to four indoor units attached. For full disclosure, the homeowner is an employee of Mitsubishi, so he certainly has a professional bias. Still, I think it’s a strong vote of confidence in the technology that a Mitsubishi employee selected whole-home heat pumps for his own house!
For the four indoor units, the homeowner installed three wall-mounted units downstairs and one mini-duct unit that served all the rooms upstairs. See the illustration below for more details on the layout. The heat pump’s capacity is 42,444 btu/hr at 5°F, compared to an estimated peak heat load of 38,798 btu/hr at 12°F. The system was installed in August 2019, and while the homeowner originally left their natural gas boiler installed and operational, when the thermostat broke last winter he decided to remove the old boiler rather than repair it.
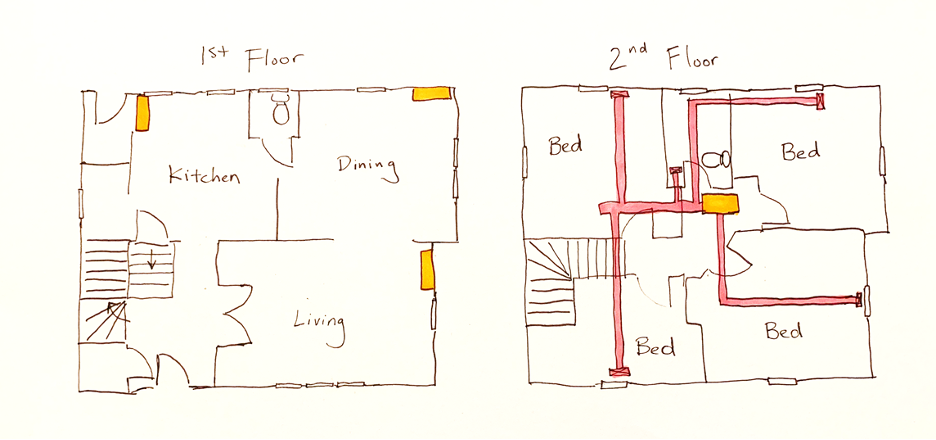
Overall, the homeowner has been happy with his heat pump, and he shared some details about his experience living with a heat pump. For example, he spray-foamed the attic after the heat pump was installed and noted that the upstairs rooms became much more responsive (i.e., quicker to heat up or cool down) after that. The homeowner also noted that the outdoor unit was mounted against the kitchen wall, and it does transmit some noise just into the kitchen. He says that this doesn’t bother him in the kitchen, but he would not want a wall mounted unit adjacent to a bedroom or living room. An alternative to wall-mounting the outdoor unit is a ground-mounted stand, which should minimize any noise that is transmitted into the home because the outdoor unit would not be connected to the home. The homeowner has a wireless temperature sensor for the ducted upstairs unit, which he can move around to control the temperature from different rooms. Normally he keeps it in the master bedroom, but if there is a guest in the guest bedroom, he can give them control of the temperature or if he is working in the office upstairs he can move the temperature sensor there.
We don’t have a typical installed cost for this project. The homeowner had a background in plumbing and electrical work, so he did some of the installation labor himself. Additionally, as an employee of Mitsubishi he was able to get a discounted scratched unit. Looking at MassCEC heat pump cost data for Suffolk County in 2019, it looks like a Mitsubishi multi-head of this capacity would cost around $19,500, although as noted above its possible the upstairs ductwork could add more to the project costs. For operating costs last year, the homeowner’s bills averaged $280 for the three coldest winter months versus $85 in September with no heating degree days. His summer bills averaged around $170 for the warmest three months.